Automobile power steering is an important safety component of automobile steering system, which is widely used in cars and large and medium-sized vehicles. Its working performance affects the operability and safety of automobile steering system. From its functional point of view, automobile steering system, The main purpose is to ensure that the driver can drive the vehicle in a straight line by controlling the system. Therefore, the steering system has a direct relationship with the safety of the vehicle on the road section. If the steering system of a motor vehicle fails, it will easily lead to driving safety problems. In view of this, the driver must ensure that the steering system is in a normal state before the vehicle goes on the road in order to improve driving safety. For this reason, it is necessary to analyze the performance of the commonly used steering system of the car.
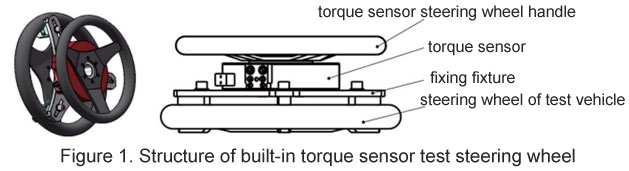
The integrated software platform of automobile steering performance test and data analysis integrates the steering performance test system of various mainstream steering wheels in the market. The system has reasonable structure design, light weight and high precision, and can be used for steering-wheel-related performance tests of various types of vehicles such as passenger cars and commercial vehicles. The test steering wheel integrated with the reaction torque sensor is recommended first, which can effectively ensure the product use accuracy and high cost performance. The shape and fixture can be customized according to user requirements to meet the national standard and enterprise standard various tests.
Features:
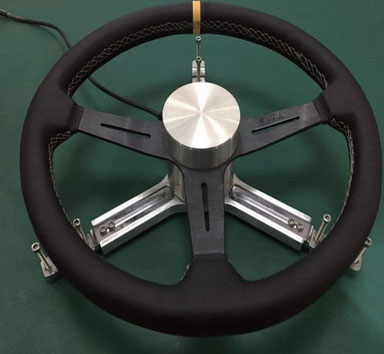
- High precision torque and angle testing
- Portable and easy to install and test
- No-disassembly steering wheel, strong versatility, suitable for different sizes of steering wheels
- It can collect data through the host computer itself
- Automatically generate test reports
Specification:
- Steering wheel torque range: 17.5-175Nm (for customers to choose)
- Steering wheel torque accuracy: ±0.1%.F.S
- Steering wheel torque resolution: 0.03Nm
- Steering wheel angle range: ±1440°
- Steering wheel angle accuracy: 0.1°
- System excitation voltage: 9-12 V
- Operating temperature range: 20~80℃
- Clamping steering wheel diameter range: 350-490mm
- Weight: 4kg (including clamping mechanism)
- Safe Overload: 200%FS
Functional principle
1. Angle signal output
The steering wheel angle signal adopts the inner core of the high-precision photoelectric encoder, and the angle resolution is less than 0.03°. One end of the photoelectric encoder is connected with the steering wheel shaft, and the other end is connected with the steering wheel sensor housing. During the test, the steering wheel sensor shaft is fixed to the steering wheel through the sensor clamp, and the steering wheel housing is fixed to the window through the disc washer fixing member, so as to ensure the output angle signal relative to the static position of the window during the rotation angle of the steering wheel. The angle signal of the encoder is stored in the ROM of the sensor itself in real time. When a power failure or shutdown occurs, the torque sensor will clean up the angle signal of the encoder.
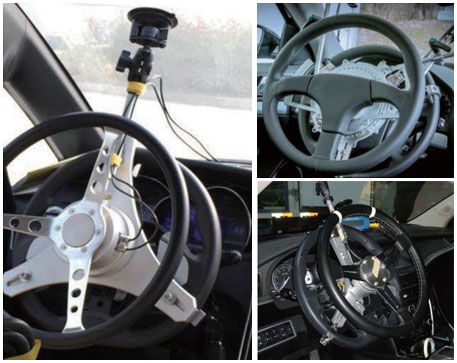
2. Angular velocity signal output
The angular velocity signal does not have a special torque sensor signal for collection and output, but differentiates the angle signal through the calculation module, and then combines the high-precision timer (sampling rate) to output the angular velocity signal. In the displacement signal acquisition module of the angular velocity calculation module, the output angular velocity signal of the steering wheel sensor must be connected to a specially configured signal conditioning module. Likewise, if a shutdown or power failure occurs, the angular velocity signal will be cleared.
3. Torque signal output
The torque signal is measured by a professionally customized dynamic full-bridge low-voltage reaction torque sensor. One end of the torque sensor is fixed with the steering wheel through the claws, and the other end is connected with the sensor joystick. In order to ensure the measurement accuracy of the torque sensor, its position is close to the steering wheel surface. The torque sensor is powered by the data acquisition module, and its output signal also needs the data acquisition module to filter and amplify the signal, and finally convert it into a standard CAN signal.