1. Foreword
The equipment level of my country's steel rolling production line is multi-level, among which the rolling mill of general level accounts for a considerable proportion. With the development of steel production, in order to improve the output and product quality of the rolling mill, it is necessary to correctly understand and use the equipment. Although the main drive system of the rolling mill, especially the universal joint shaft, has a large safety factor, accidents such as component breakage still occur from time to time. This is related to the torsional vibration of the instantaneous sharp increase in the torque of the drive shaft caused by shock and vibration during rolling. The author used the metallurgical measuring vehicle to measure the torque value and the torsional vibration of about 30 sets of rolling mills and auxiliary equipment drive shafts in 21 factories. On this basis, the fast Fourier analysis method is used to analyze the spectrum of the measured data, analyze the factors that cause torsional vibration, and propose measures to prevent torsional vibration. This has guiding significance for understanding the torsional vibration phenomenon in the rolling process, using the equipment correctly and avoiding accidents.
2. The Measurement Method and Principle of Torque
At present, the non-electrical measurement method is mainly used to measure the torque value, and the strain gauge is directly pasted on the surface of the transmission shaft to form a measurement bridge, as shown in Figure 1.
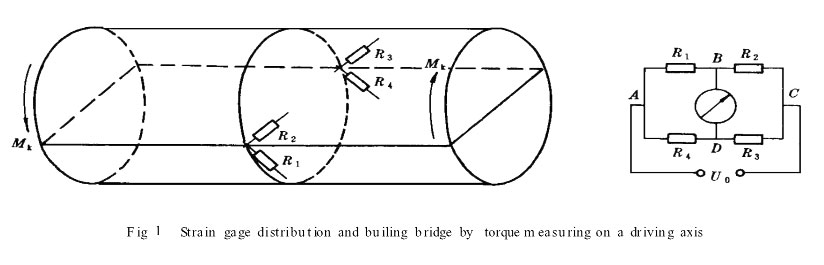
The torque value is calculated by measuring the shear strain or shear stress due to the action of the torque with the corresponding torque sensor. The advantage is that the torsional deformation of the transmission shaft can be directly measured, and the indirect influence factors calculated by the power and speed of the main motor are reduced.
The torque and strain have a linear relationship. The key to torque measurement is to solve the problem of signal transmission. At present, the commonly used torque signal transmission methods include wired transmission and wireless transmission. Wired transmission is to use slip rings and brushes to lead the electrical signal on the drive shaft to the measuring instrument. The metallurgical measuring vehicle is equipped with wireless transmission, the system with torque sensor is shown in Figure 2. The mechanical strain on the drive shaft causes the resistance of the strain gauges attached to the shaft to change, unbalance the bridge and generate a voltage proportional to the torque value. The voltage is converted into an output frequency proportional to the torque value by an oscillator (using the principle of frequency modulation), the signal is sent from the sending coil to the receiving coil, and the signal is demodulated and converted into a voltage signal by the discriminator for recording and display. The measuring bridge, oscillator and sending coil are all installed on the measured shaft to rotate with the shaft, which avoids the difficulty of rotating the shaft lead and the influence of the contact resistance of the contact slip ring.
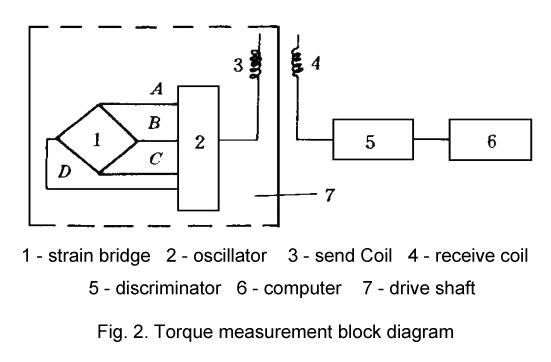
3. Measurement Results and Analysis
The vibration generated in the measurement process is analyzed by the fast Fourier analysis method.
When biting into the rolling piece, due to the impact of biting, the pressure on the frame and the torque on the drive shaft all have a considerable vibration waveform. Its vibration frequency is concentrated in the range of 20 times. This is true whether it is blooming mill, medium plate rolling mill, cold rolling mill or continuous rolling mill. The vibration time is within 2s.
The torque alternating cycles generated by vibration are mostly asymmetric (Fig. 3). This torque vibration can cause a sudden increase in torque on the shaft. When the peak value Mmax of the torque exceeds 215 times the rated torque value of the transmission shaft, the transmission shaft and its supporting parts are in great danger, and it is easy to cause the shaft to break.
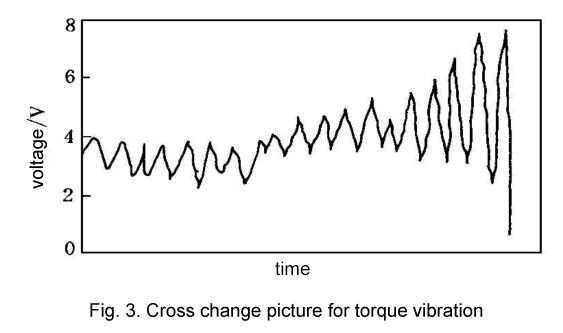
For example, in the measurement of the steel rolling mill, when three steels were rolled at the same time, the torque value exceeded the rated value by more than 3 times, causing the fracture of the drive shaft, see Figure 4. But often when it does not exceed 215 times, the accessories are damaged.
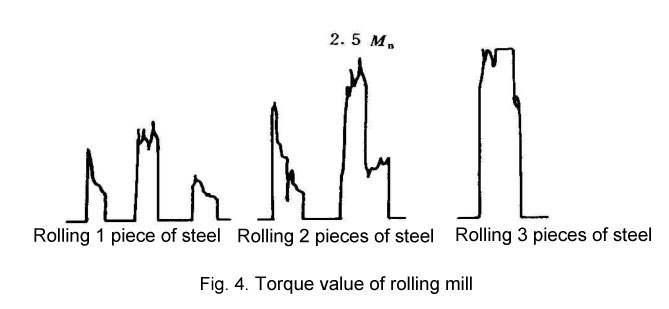
For example, when a 1 200 mm medium plate cold rolling mill in a non-ferrous metal processing plant is rolling a titanium alloy sheet, the main drive shaft and universal joint shaft frequently occur on the main drive shaft and universal joint shaft. At this time, the torque value on the universal joint shaft is 2132 times the rated torque value, which causes the accident of broken pins, and obvious stripes appear on the surface of the cold-rolled sheet, which affects the surface quality. The maximum torque during vibration does not exceed 215 times the rated torque, which indicates that there are still other factors. The torque amplification factor Ka (generally designed around 5) can be used to illustrate this phenomenon.
When Ka exceeds the design safety factor, the component may break. When the torsional vibration occurs, K . The maximum value is 515, see Table 1.
Number | Vibration frequency | Mmax Mo | Mmax Mu | Vibration duration |
51 | 22150 | 2180 | 2114 | 0140 |
54 | 22150 | 1180 | 1113 | 0140 |
105 | 17114 | 2148 | 3178 | 0170 |
106 | 18160 | 1144 | 1107 | 0143 |
115 | 20100 | 1138 | 2104 | 0140 |
122 | 19140 | 5100 | 5150 | 0167 |
141 | 19130 | 3170 | 2167 | 0157 |
150 | 15122 | 4179 | 3140 | 0192 |
On different types of rolling mills, when the rolling mill suddenly bites the steel during the torque measurement, the main drive system produces obvious shock vibration, as shown in Figure 5. At this time, the peak value of the upper universal joint shaft and the peak value of the lower universal joint shaft are respectively 2129 and 2143 times the rated value. Although no fracture occurs, such a large fluctuation stress amplitude and a certain number of variable stress cycles (vibration Frequency 5~6 times) will accelerate the fatigue damage of the shaft and shorten the service life of the parts.
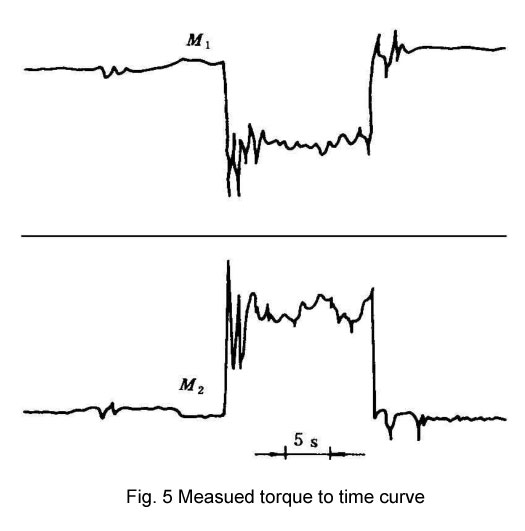
Similarly, during low-temperature rolling on small and medium-sized continuous rolling mill, vibration occurs due to stacking steel, and its maximum torque reaches 7719% of the rated value (see Table 2), which does not exceed 215 times the rated torque, but it continues for a long time. Fatigue damage will be formed, which is detrimental to the equipment.
Number | Frequency | Status | Basic amplitude/Nm | Amplitude increase value/Nm | Amplitude combined value/Nm | Remark |
1 | 0188 | stack | 1332 | 1806 | 3138 | low temperature |
2 | 0158 | stack | 2389 | 740 | 3129 | normal temperature |
3 | 0167 | accident | 2072 | 888 | 2961 | normal temperature |
4 | 0183 | accident | 1954 | 1095 | 3049 | normal temperature |
4. Factors Causing Torsional Vibration and Preventive Measures
4.1 Factors causing torsional vibration
- Impact and slippage when the rolled piece bites. The temperature of the rolling piece is too high, the iron oxide scale is too thick, and the rolling piece is unstable to bite and slip. The shape of the head of the ingot is irregular, the temperature is too low, the acceleration after biting the steel is too fast, and the balance between the applied torque, the internal torque on the shaft and the motor torque is destroyed, which makes it difficult to bite.
- Slow down when throwing steel.
- The pressing amount is too large.
4.2 Conditions under which torsional vibration causes parts to break
- When the Ka that produces torsional vibration exceeds the safety factor of the main drive system component (generally around 5), the component may break.
- The size design of the transmission shaft or components is not suitable, or the material grade used is not enough, or the heat treatment process system for it is not appropriate, so that the load capacity that the component can withstand fails to meet the specified requirements and breaks.
- When the maximum torque of the transmission shaft is greater than 215 times the rated torque, the shaft will be broken.
4.3 Measures to prevent or reduce torsional vibration
In order to prevent or reduce torsional vibration and breakage of transmission system components, the relevant T factory shall take corresponding technical operation measures for the causes of torsional vibration. For example, in rolling operations, strictly control the rolling stock Biting speed), adopt low-speed biting to avoid rapid acceleration; master the reduction of each pass; reduce the rolling speed to avoid slipping; control the temperature of the rolling piece to avoid excessively thick oxide scale; when the surface temperature of the rolling piece When it is too high, appropriately reduce the rolling speed or prevent the reduction from being too large, and prohibit forced rolling to cause long-term slippage and strong torsional vibration. Some parts often break, and it is necessary to improve the load-bearing capacity of the parts and improve their Heat treatment process or improve material grade.
5. Conclusion
- In the process of measuring torque value of the rolling mill transmission system, it was found that the bite impact and slippage of the rolling stock may produce torsional vibration. Based on a large number of measured data, the spectrum analysis is carried out by the fast Fourier analysis method, and it is shown that the rolling force and torque values simultaneously increase exponentially in an instant when torsional vibration occurs. Since the basic amplitude of the torque is large, if a larger superimposed amplitude is generated, the danger is even greater. The maximum torsional vibration of the rolling mill drive system listed is 213 to 215 times its rated torque value. This is one of the important reasons for the breakage of transmission system components.
- The frames and transmission systems of different rolling mills have different vibration frequencies and durations when torsional vibration occurs. The vibration frequency of the transmission shaft torque is generally within 20 times, and the vibration duration is 1~2s.
- The reasons for the occurrence of torsional vibration and the countermeasures adopted in the production operation are analyzed, which are of great significance to the correct use of the equipment and the prevention of accidents. realistic meaning.