Torque is an important parameter in motor test. Especially in motor efficiency evaluation, torque is an indispensable measured value. The accuracy of motor torque measurement is directly related to the correctness of motor efficiency evaluation.
Torque is divided into static torque and dynamic torque. Static torque refers to the torque that does not change with time or changes very little and very slowly, including static torque, constant torque, slowly changing torque and micro-pulsation torque. The value of static torque is a constant, and the transmission shaft does not rotate. The value of constant torque is a constant, but the transmission shaft rotates at a constant speed, such as the torque when the motor is working stably. The value of slowly varying torque changes slowly with time, but in It can be considered that the torque value is constant in a short period of time. The instantaneous value of the micro-pulsation torque has a small pulsation change.
Dynamic torque refers to the torque that change greatly with time, including vibration torque, transition torque and random torque. The value of vibration torque fluctuates periodically. Transition torque is the torque transformation process when machinery is converted from one working condition to another. Random torque is an uncertain and irregular torque.
The motor torque measurement methods currently used can be divided into balance force method, transfer method and energy conversion method according to the measurement principle.
1. Balance Force Method
For a transmission mechanical component in a state of uniform speed, there must be a pair of torques T and T' on the main shaft and the body at the same time, and the two are equal in magnitude and opposite in direction. The method of measuring T on the main shaft by measuring T' on the body is called the balance force method. Let F be the force on the force arm and L be the length of the force arm, then T'=LF. T' and T can be obtained by measuring the force F and the force arm L. The advantage of the balanced force method is that there is no problem of transmitting torque signals, and the force F on the force arm is easy to measure. The disadvantage is that the measurement range is only limited to a uniform speed working state, and the measurement of dynamic torque cannot be completed.
2. Transfer Method
The transfer method utilizes that the physical parameters of the elastic element will change to some extent when the torque is transmitted. Torque is measured using this change corresponding relationship with torque . According to different physical parameters, the transfer method can be further divided into magnetoelastic type, strain gauge type, vibrating wire type, photoelectric type, etc. Currently, the transfer method is the most widely used in the field of torque measurement. According to the different principles of transfer methods, different types of torque sensors are also produced in turn.
2.1 Photoelectric Type
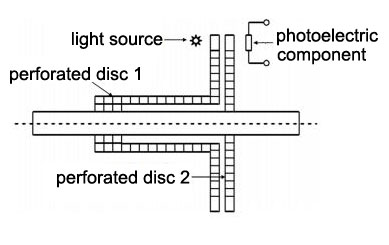
Two disc-shaped gratings with the same number of openings are fixed on the rotating shaft, and the photoelectric element and the fixed light source are fixed on both sides of the grating respectively. When there is no torque action on the rotating shaft, the light and dark stripes of the two gratings are staggered, completely blocking the light path, no light shining on the photosensitive element, and no electrical signal is output. When there is torque action, the cross-sections of the two disc-shaped gratings generate relative rotation angles, the light and dark stripes partially overlap, and part of the light shines on the photosensitive element through the grating to output electrical signals. The larger the torque value, the larger the torsion angle, the greater the light intensity on the photosensitive element, and the greater the output electrical signal. The magnitude of the applied torque can be measured by measuring the output electrical signal.
The advantages of photoelectric torque measurement are fast response speed and real-time monitoring of torque. Its disadvantages are complex structure, difficult static calibration, poor reliability, poor anti-interference ability, and measurement accuracy is greatly affected by temperature changes. This method is not suitable for motor torque measurements on just-started and low-speed shafts.
2.2 Magnetoelectric Torque Measurement Method
Two identical gears are installed on the elastic shaft. The magnetic core and the coil form a signal acquisition system. A small gap is reserved between the tooth tip and the magnetic core. When the shaft rotates, two alternating electromotive forces are induced in the two coils respectively. And the alternating electromotive force is only related to the relative position and intersection position of the magnetic cores of the two gears, and the corresponding torque value can be obtained by detecting the magnitude of the electromotive force.
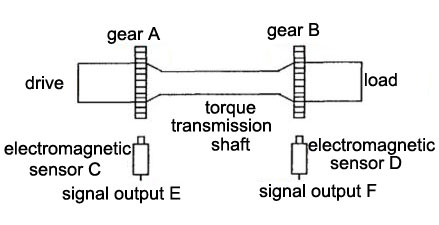
The advantages of magnetoelectric torque measurement are high precision, low cost and reliable performance. It is non-contact measurement, that is, it does not require power supply and intermediate transmission links; its disadvantages are complex structure, limited frequency response, difficult to manufacture, and long response time. The size and mass of the corresponding torque sensor are large, the signal is small at low speed, and dynamic balance is difficult at high speed. The magnetoelectric torque measurement method is suitable for measuring the motor torque that can produce a large angular displacement, and can measure the starting and low-speed torque. Due to its poor dynamic characteristics, it is not suitable for torque measurement of high-speed rotating shafts.
2.3 Vibrating Wire Torque Measurement Method
Using the functional relationship between the natural frequency of the vibrating string and the tension, the force is converted into electric quantity, and the electric quantity value is first converted into the force, and then the corresponding torque value is calculated.
The advantage of vibrating wire torque measurement is that it can directly use the transmission shaft as the torsion shaft for measurement. The frequency signal transmission method is adopted, and the anti-interference performance is good. The sensor part is separated from the force measuring shaft, which is convenient for measurement on ships or vehicles. Its disadvantage is the structure Complex, low sensitivity, low measurement accuracy, and high requirements for elastic deformation of the elastic shaft. This method is suitable for torque measurement of large shafts but not for high-speed shafts.
2.4 Magnetoelastic Torque Measurement
The magneto-elastic torque measurement method refers to a method of measuring torque by using the magneto-elastic effect of ferromagnetic materials and other alloy materials. When torque is applied to the elastic axis of ferromagnetic materials in a magnetic field, the change in magnetic permeability will reflect The change in the magnetization of a ferromagnetic material, and therefore the torque signal can be obtained by measuring the change in magnetic permeability.
The advantages are high sensitivity, good stability, non-contact measurement, high output power, fast response speed, good overload capacity, convenient installation & use, strong anti-interference ability, simple structure & circuit, and can work in harsh environments. The disadvantage is that there is an "arc modulation" error, which limits its application. There is an inherent deviation in the magnetic permeability distributed along the circumference of the torsion axis, and its measurement accuracy is relatively low, only the stress value of the magnetostrictive layer material is measured. There is still a deviation from the required torque value. The magneto-elastic torque measurement method is widely used in the fields of ship power plants, steel rolling, oil drilling rigs and CNC locomotives.
2.5 Strain gauge type torque measurement
The torque will cause a certain strain to the transmission shaft, and this strain has a proportional relationship with the magnitude of the torque, so the magnitude of the corresponding torque can be detected by the resistance strain gauge. When the transmission shaft is subjected to torque action, torsional deformation will occur, and the maximum shear strain is generated in the direction of 45° to the axis. Paste the resistance strain gauge in this direction, torque sensor will detect the torque of the transmission shaft.
The advantages of the strain torque measurement method are simple structure, high sensitivity, strong adaptability, low cost, easy operation, mature technology, wide application range, high measurement accuracy, fast response speed, stable and reliable performance, good temperature compensation performance, adaptable Harsh environment. The disadvantage is that humidity, temperature, binder and other factors will affect the accuracy of the measurement, and the anti-interference ability is poor. This method is not suitable for torque measurement of high-speed rotating shafts.
3. Energy Conversion Method
The energy conversion method refers to the indirect measurement of torque by measuring other parameters such as thermal energy and electrical energy according to the law of energy conservation.