A company has 4 slag powder production lines with an annual output of 600, 000 tons, equipped with 2 700kW reducers. The machine is equipped with monitoring points, but not equipped with corresponding software. In the previous year, due to various reasons, problems such as gear breaking of the reducer and fracture of the vertical shaft occurred, resulting in great losses. For this reason, a set of monitoring system with torque sensor is added according to the original design characteristics of the reducer. The monitoring system has two functions: First, it can give early warning in the event of equipment failure. Identify the type of failure. The second is to reduce or even avoid the impact of other equipment failures on the vertical mill reducer by means of process adjustment or equipment maintenance after predicting the failure, protect important equipment.
1. Composition and Characteristics of Reducer Monitoring System
Vertical mill reducer monitoring system is mainly composed of speed sensor, torque sensor, XY direction vibration sensor, acceleration sensor, vibration detection unit, monitoring system and analysis software. There are 8 monitoring points installed in the reducer.
The main feature of this monitoring system that is different from the traditional monitoring system is that in addition to recording the traditional vibration signal, a new torque detection system is installed. While analyzing the frequency domain information of the vibration signal, the frequency spectrum of the torque signal is also analyzed. The torque signal is reliably recorded by the non-contact measurement of the telemetry sensor. To obtain the torque signal, a resistance strain gauge, a signal amplifier and an antenna loop are installed on the drive shaft (see Figure 1). The antenna loop can be detached and installed on existing equipment. After the power supply voltage is connected, the signal data is read out through the antenna receiver fixed on the machine tool. The torque signal is one of the most important signals. The information it provides includes: equipment operating status, dangerous overload, torsion frequency, etc.
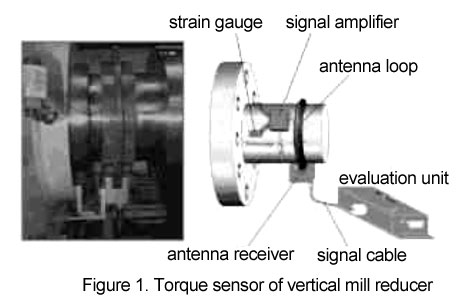
Every important part of the equipment has its own rotation and meshing frequency. Analyze the torque curve, if there is obvious periodic vibration, then analyze the wear and damage degree and cracking trend of equipment components according to the natural frequency of the equipment, prepare spare parts as soon as possible, and arrange maintenance. Since the torque value of the reducer directly reflects the operating condition of the equipment, the torque signal must be analyzed first. In order to check whether the torque signal is abnormal, the system has set up 5 types of torque alarm signals, and simply analyzed the reasons for the torque alarm (see Table 1).
Alarm name | Alarm reason |
Torque maximum value alarm | Reducer damage: The grinding wheel bearing is damaged, and the temperature of the grinding wheel bearing rises; Foreign matter enters inside the grinding disc, simultaneous impact alarm |
Torque Mean Alarm | Excessive feeding amount of vertical mill and overload operation: When the machine is started, the police warn that there are too many materials for the grinding disc, and the resistance is excessive; The phenomenon of full rotation occurs, and the material cannot be discharged in time; the grinding pressure is too large: The grinding bearing is damaged, often accompanied by the rise of bearing temperature and the phenomenon of low speed |
Torque peak shock alarm | Large clutch clearance when starting the mill: The metal foreign body is inserted into the mortar plate Parts such as the mill lining plate fall into the grinding disc; Reducer damage |
Negative torque alarm | The shape of the material bed is not good, the finishing machine is unstable, and the turning machine itself vibrates greatly; The reducer has broken clock and broken teeth |
Dynamic value alarm | The material bed is not well formed, the mill is unstable, and the mill itself vibrates greatly: Analysis of the characteristic curve of the appearance of the seam front, the fracture and the partial shedding of the welding layer; There are pits and cracks in the lining of the grinding disc, and the analysis is based on the characteristic curve |
2. Reducer Fault Judgment and Case
For monitoring alarm events, it is necessary to analyze in combination with the production process to confirm which are caused by changes in process parameters and which are caused by equipment failures. Under normal circumstances, combined with the actual situation of production and operation, referring to the trend changes of software data, firstly form an offline torque trend according to the database, analyze and check the change trend of the torque signal; then use the torque signal and acceleration signal detected by the torque sensor to perform time domain, frequency Domain analysis, confirm the location of the fault point step by step: The monitoring system analyzes the eigenvalues from the acceleration and envelope signals, gives the abnormal phenomenon of the equipment and the change of the operating state, and analyzes the location of the fault through the frequency domain characteristics.
Accident case 1:
In June 2010, some eigenvalues of the torque signal of Line 1 tended to increase, and the dynamic value alarms increased. Due to the complex situation, the relevant data is sent to foreign countries, and they comprehensively analyze the torque. The torque characteristic analysis diagram is shown in Figure 2.
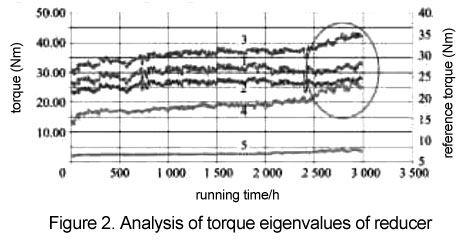
Number | Characteristic parameters | Maximum value | Minimum value | Average value | Standard variance | Correlation value |
1 | torque average value (kNm) | 28.35 | 22.87 | 26.22 | 1.16 | 1.00 |
2 | torque average value (kNm) | 28.35 | 22.87 | 26.22 | 1.26 | 1.00 |
3 | maximum torque (kNm) | 43.17 | 29.49 | 36.52 | 2.64 | 0.78 |
4 | peak torque (kNm) | 28.05 | 12.65 | 19.38 | 2.87 | 0.50 |
5 | standard deviation | 4.30 | 1.91 | 2.85 | 0.49 | 0.43 |
Number 1&2 in the table is the average torque value, which is a reference curve to identify whether the overall load change of the mill is caused by the process operation change. Use the coordinates on the right. 3 is the maximum torque value, 4 is the peak torque value, and 5 is the standard deviation value. 3, 4, and 5 are actual curves. Use left coordinates. The analysis results show that after 2500 hours of operation, the eigenvalues of each point obviously exceed the normal range and show an increasing trend.
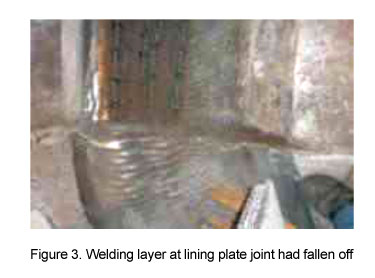
Firstly, referring to the acceleration signal of each point, analyze the eigenvalue trend of the acceleration signal, and find that the acceleration signal of each point has no obvious trend change. Analysis and judgment, the reason for the change of torque characteristic value may be caused by external factors of the reducer. Combined with the characteristic trend of the torque signal, the time domain value of the torque signal is further analyzed, and the characteristic frequency obtained before is combined with the mill's own structure. Characteristics, it is judged that the possibility of failure of the grinding disc is very high.
According to the information provided by the warning, the machine was stopped to check the No. 1 grinding disc, and it was found that the welding layer at the joint of the lining plate had fallen off into pits (see Figure 3), resulting in irregular depressions. Quickly organize maintenance and repairs to repair the hidden dangers of the equipment to avoid further damage.
Accident case 2:
A large number of shock alarms of torque peaks occurred during the operation of the vertical mill, some of the torque characteristic values showed an increasing trend, and there was regular vibration on site. Referring to the acceleration signal of each point, analyzing the trend of the eigenvalues of the acceleration signal, it is found that the acceleration signal of each point has no obvious trend change. It is analyzed and judged that the reason for the change of the torque characteristic value may be caused by the external factors of the reducer. Combined with the analysis of other parameters, it is predicted that there are foreign objects such as hanging plates in the mill, causing the vertical mill to vibrate. There should be no problem with the reducer itself. When the vertical mill was stopped for inspection and processing, it was found that there were foreign objects such as hanging plates at the junction of the grinding wheel and the grinding disc, which had been squeezed and deformed.
After the accident was dealt with in time, production was resumed, and all torque curves returned to the normal range.
3. Conclusion
After the installation and operation of the detection system, the process parameters are actively adjusted according to the curve changes to reduce the damage to the equipment caused by the vicious impact, avoid the damage of the reducer and other equipment, and play a good auxiliary role.
It has been proved by practice that the installation of the torque sensor and the trend analysis of the parameters of the time-domain waveform of the torque and vibration signals can make an overall judgment on the operation of the machinery and equipment. According to the actual situation, the main components of the vertical mill are simply diagnosed, which enriches the identification methods for the complex and changeable production site. For equipment failure prediction and timely processing, the deterioration of equipment failure is avoided, and it has played a significant role in protecting large and valuable equipment such as reducers.