Basic Introduction of Torque Sensor
Torque is the most frequently involved parameter in the rotating power system. In order to detect the rotating torque, the torsion angle phase difference sensor is used more. The sensor is equipped with two sets of gears with the same number of teeth, shapes and installation angles at both ends of the elastic shaft, and a proximity (magnetic or optical) sensor is installed on the outside of the gears. When the elastic shaft rotates, the two sets of sensors can measure the two sets of pulse waves, and the amount of torque borne by the elastic shaft can be calculated by comparing the phase difference between the front and rear edges of the two sets of pulse waves. The advantages of this method: the non-contact transmission of the torque signal is realized, and the detection signal is a digital signal.
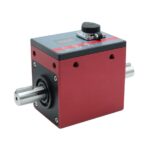
The relatively mature detection method of torque test is strain electrical measurement technology, which has the advantages of high precision, fast frequency response, good reliability and long life. The special torsional strain gauge is pasted on the elastic shaft to be measured with strain glue to form a strain bridge. If the working power is supplied to the strain bridge, the electrical signal of the elastic shaft to be torsion can be tested. This is the basic torque sensor pattern. But in the rotating power transmission system, the most difficult problem is how to reliably transmit the bridge pressure input of the strain bridge on the rotating body and the detected strain signal output between the rotating part and the stationary part. ring to complete. Since the conductive slip ring is in frictional contact, it is inevitable that there will be wear and heat, thus limiting the rotational speed of the rotating shaft and the service life of the conductive slip ring. And due to unreliable contact, the signal fluctuates, resulting in a large measurement error or even unsuccessful measurement.
In order to overcome the defects of the conductive slip ring, another method is to use the method of radio telemetry: amplify the torque strain signal on the rotating shaft and convert V/F into a frequency signal, and transmit it from the rotating shaft by means of radio transmission through carrier modulation. To the outside of the shaft, and then use the method of radio reception, you can get the signal that the rotating shaft is twisted. The energy supply on the rotating shaft is a battery fixed on the rotating shaft. This method is called a telemetry torque meter.
Common Problems and Solutions of Torque Sensor Industry
At present, there are four problems in the measurement of torque sensors: first, the structure of the sensor is different; second, the adapters are not uniform; third, online measurement is restricted; fourth, the universality of torque measuring instruments is not good. In view of these problems encountered in the process of torque measurement and the actual needs of torque measurement in reality, we can try to take measures from the following aspects.
1. Unified sensor manufacturing standards
Revise the current industry standards or formulate special industry standards for torque sensors to unify or limit the structure of the input and output terminals of the torque sensor, standardize the manufacturing standards of torque sensors, and meet the needs of torque measurement in all walks of life. Unified standards are the key to solving the problem of torque sensor measurement. The production and manufacturing standards are unified, and then the problems of connectors and online measurement will be alleviated.
2. Standardize the processing size of connectors
For the machinery manufacturing industry, there are tens of thousands of standard parts, all of which have corresponding standards and requirements. For the connection parts of the torque sensor, the existing standard parts should be used as much as possible. If the requirements for use are not met, the corresponding dimensions can be formulated, and the use of materials, geometry, strength, heat treatment requirements, etc. should be uniformly specified. This can also be limited in the current industry standards, so as to facilitate the manufacture of manufacturers and the selection and use of customers, and at the same time minimize the superposition of adapters to avoid uncertainty components.
3. Research and development of online measurement standards
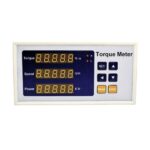
Research and develop relevant standards for online measurement, so that the device can adjust parameters such as sampling frequency and sampling period; the device can have multiple ranges; there is a fixed way to connect with the tested equipment to reduce the influence of human factors; there is an online feedback compensation system, It is guaranteed that the serial connection of online torque meters will not bring new influences or the influences are very small; the system is implanted in the wireless WiFi mode or Bluetooth mode to ensure disturbance-free dynamic detection, etc., to realize the correct production and detection.
4. The universality of the prescribed measuring instruments
For example, in the field of force value, since the manufacturing principles of the sensors are the same, some secondary instrument can well adapt to the requirements of various types of force sensors, thus forming a universal force measurement system. The application of force value measurement in production and life is very extensive and can be seen almost everywhere. Therefore, we should learn from the form of force measuring instruments, develop corresponding types of torque measuring instruments for torque sensors in different application fields, and match with general-purpose instruments as much as possible, reduce the complicated work of customer selection, and improve the efficiency and accuracy of measurement and measurement. Spend. While ATO Torque Sensor is in line with the industry benchmarking international brands, but also has new products independently developed. Such as a dynamic torque/power/speed three-in-one measuring instrument with an electronic display. While it is detecting torque, power and rotational speed are also measured. And the values are displayed on the electronic screen in real time, making operation and display easier. It is especially suitable for experimental use in testing experiments.